Прикамские братья по металлу
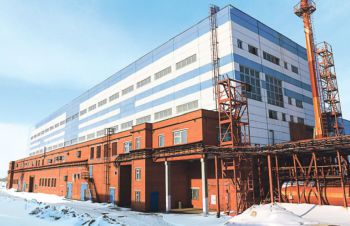
14 марта 1936 года на соликамском магниевом заводе был произведён первый магний-сырец, и отлита первая чушка из него.
Спустя семь лет первую чушку магния получат и на Березниковском магниевом заводе. С тех пор два род- ственных предприятия, как два брата, пойдут по жизни рядом, помогая друг другу, но при этом развиваясь каждый в своём направлении. Накануне юбилея журналисты пресс-центра «Ависмы» решили заглянуть к «старшему брату» и узнать, чем живёт почти 2,5-тысячный коллектив ОАО «СМЗ» сегодня, чтобы рассказать об этом читателям «Металлурга», как говорится, из первых уст.
ВСЁ ДЛЯ ПОБЕДЫ
Конечно, история СМЗ началась задолго до выпуска первого слитка магния - с открытия в 1925 году Верхнекамского месторождения калийно-магниевых солей. Спустя 6 лет на заседании бюро Уралобкома ВКП(б) было принято решение о строительстве в Соликамске, близ первого калийного рудника, карналлито-магниевого комбината. Само строительство началось в мае 1934-го. За полтора года были возведены основные корпуса: цех вращающихся печей, первая и вторая серии электролиза. С пуском завода не затягивали, он состоялся ровно 80 лет назад, едва заработал первый электролизёр.
А первая чушка магния весила 2,5 кг. Полностью первая линия электролиза вошла в строй летом 1936 года. Тогда же в цехе №5 по производству химикатов начался выпуск бертолетовой соли, его первым начальником был не кто иной как Клавдий Иванович Циренщиков, возглавивший спустя годы Березниковский магниевый завод.
Уже к 1939 году СМЗ освоил производство магниевых сплавов для авиации. В 1941 году завод выводится из состава калийного комбината и становится самостоятельным предприятием со своим директором - Дмитрием Бачуриным. А потом грянула Великая Отечественная вой- на. Сотни кадровых рабочих ушли на фронт, на их место встали женщины и подростки. Для борьбы с захватчика- ми Родине требовалось много магния, поэтому оперативно запускается вторая серия электролиза.
В Соликамск приходят сотни вагонов с оборудованием Днепровского магниевого, Тихвинского глинозёмного и Волховского алюминиевого заводов, начинается монтаж третьей серии электролиза и ТЭЦ мощностью 10 МВт. На строительство прибывают без малого 2,5 тысячи человек из тех, кто оказался негоден к фронтовой службе, в том числе жители Средней Азии. К 1944 году выпуск продукции удаётся повысить с 3 до 7,5 тыс тонн. Интересный факт: на производство самолётов эскадрильи «Соликамский рабочий» коллектив завода собрал 700 тыс руб.
Согласитесь, что всё написанное выше едва ли не слово в слово (за исключением дат) повторяет ход событий, изложенных в книге «Сражение за Победу в уральском тылу» и связанных с возведением и пуском Березниковского магниевого завода. Да-да, в Соликамске, как и в Березниках, рабочий посёлок из бараков соседствовал с промплощадкой.
РЕВОЛЮЦИОНЕР СОЛЯКОВ
Совершенно не исключаю, что эта фамилия вам ни о чём не говорит. До поездки на СМЗ не знал её и я. Но именно Степану Павловичу Солякову и Соликамский магниевый, и «Ависма» обязаны многим. Первый в Прикамье заслуженный изобретатель РСФСР по праву носит титул революционера цветной металлургии.
В 1946 году на СМЗ во главе с Соляковым создаётся опытный цех - первый случай в отрасли. Если в общем, то именно здесь были разработаны основные базовые технологические процессы, используемые магниевыми и титановыми предприятиями стран СНГ. В частности, инженеры этого цеха создали и испытали новые, более производительные и менее энергоёмкие электролизёры. Технология выборки и транспортировки магния-сырца при помощи вакуум-ковша тоже родом отсюда.
Степану Солякову принадлежит авторство изобретения хлоратора для обезвоживания карналлита. Всеми новация- ми, знаниями, опытом «старший брат» охотно делился с «младшим». Как вспоминает ветеран опытного цеха Николай Мальцев, к 1957 году на СМЗ не осталось оборудования, предусмотренного первоначальным проектом.
Спустя ещё 10 лет произведённые в Соликамске магний и сплавы из него уже соответствуют лучшим мировым образцам. Завод начинает выпуск магний-циркониевых лигатур для авиакосмического комплекса, протекторов для защиты от коррозии морских судов и газопроводов. Но для опытного цеха и работавших с ним институтов это была только разминка. Впрочем, об этом чуть позже.
ТАКИХ В СТРАНЕ БОЛЬШЕ НЕТ
Начальник цеха электролиза магния СМЗ Сергей Новиков не зря проработал здесь 30 лет. Уж он как никто умеет по беглым взглядам приехавших журналистов понять, о чём они думают.
Сергей Новиков: - Понимаю, что при виде здания, которому 80 лет, и совсем не таких масштабных цеховых площадей, как у вас на «Ависме» , может сложиться обманчивое впечатление. Наше производство, хоть и небольшое, но современное. В целях улучшения качества продукции агрегаты постоянно модернизируются. Оборудования нам по нынешним задачам хватает, хотя у нас и электролизёры в два раза менее мощные, чем на «Ависме» , и печи для обезвоживания карналлита за исключением одной не кипящего слоя, а вращающиеся. В былые времена мы производили до 17,5 тыс тонн магния-сырца, сейчас на 3 тысячи меньше: сырья не хватает, поскольку теперь с соликамской карналлитовой фабрики «Уралкалия» карналлит поставляют не только нам, но и на «Ависму» по известной всем причине. Но друзьям же надо помогать!
Особая технологическая гордость начальника цеха - печь непрерывного рафинироческим насосом, изобретённая и созданная специалистами завода. Этот агрегат выполняет задачу, которая раньше выпадала трём разным устройствам. Магний-сырец до 10 тонн за раз заливается в ПНР, рафинируется, после чего попадает на литейный конвейер, где установлены изложницы под чушки массой как 8, так и 12 кг. Обслуживают этот процесс всего три человека.
Кстати, если вы задались вопросом, почему на СМЗ делают оборудование, а не приобретают его, то ответ прост: на долю полутысячного коллектива цеха электролиза магния даже при сокращённом выпуске приходится свыше 60% производства товарного магния в России. Аналогичных Соликамскому заводу предприятий в стране больше нет, а значит, нет речи о каком-то типовом оборудовании.
ВОЗВРАЩЕНИЕ ЧЕРЕЗ ПОЛВЕКА
Что касается другой продукции соликамских металлургов - титана губчатого, то здесь СМЗ закрывает пример- но 5% российского производства, уступая основной объём «Ависме» . С титановой губкой в Соликамске сложилась крайне любопытная история: разрабатывать базовую производственную технологию здесь начали в 1956 году, а первую опытную партию готового продукта по- лучили лишь в 2008- м. Как так могло получиться?
Николай Мальцев, ветеран СМЗ: - В 1956 году, когда я только-только пришёл работать в опытный цех, команда специалистов во главе с Павлом Соляковым разрабатывала новую технологию получения тетрахлорида титана путём вскрытия сырья в расплав- ленных средах. Такой подход позволял получить продукт куда более высокой чистоты, чем прежде. Министр цветной металлургии Пётр Ломако дал задание на основе полученных выкладок сделать опытную установку хлорирования в расплаве. К 1961 году она была сделана, но к тому моменту на БТМК уже начали производить губку, поэтому Ломако принял решение, внедрить расплавные титановые хлораторы и запустить в Березниках крупнотоннажное производство титана.
К теме собственного титанового производства в Соликамске вернулись в начале нулевых. Производить губчатый титан на СМЗ из собственного тетрахлорида титана магниетермическим способом оказалось лучшим решением, чем перерабатывать тетрахлорид в диоксид титана.
В качестве основы для технического сотрудничества с «Ависмой» стало внедрение более производительного аппарата. Такой аппарат в перспективе может стать прототипом для строительства нового корпуса на березниковском предприятии. Но как проявят себя все нюансы «пятитонной» технологии в новом исполнении?
Это нужно было проверить в промышленной эксплуатации. Над местом возведения цеха долго не размышляли. В 2006 году началось проектирование и строительство, в 2008-м проведён первый процесс. В этот период на СМЗ в цех по производству губчатого титана (№9) пришёл бывший начальник цеха №35 «Ависмы» Андрей Патраков.
Андрей Патраков, начальник цеха №9 СМЗ: - Генпроектировщиком проекта стал Российский институт титана и магния (РИТМ), который с самого начала проектирования учитывал опыт «Ависмы» . Под новый цех разработали семи-тонный аппарат, конструкция которого заметно отличалась от пятитонного. Весь основной костяк кадровых рабочих также был подготовлен на березниковском предприятии. Если бы не было заинтересованности нашего соседа, нам было бы гораздо сложнее. А так запустились достаточно легко. В итоге выяснилось, что ничего сверхъестественного более крупный агрегат не дал. С увеличением габаритов блока увеличивается длительность технологического процесса, возникают особенности его ведения и переработки блоков для обеспечения требований ГОСТа. Мы-то уже привыкли с ними работать, а вот «Ависма» , если и будет строить новый корпус, учтёт наши наработки.
В сравнении с масштабами нашего цеха ВиД аналогичное производство у соликамцев можно назвать миниатюрным. Су- дите сами: 8 печей восстановления, 10 печей дистилляции. Да и то из них в работе только половина. Проектная производительность первой очереди - 2,5 тыс тонн губчатого титана в год (у нас примерно в 20 раз больше).
Но зато получаемая губка не менее высокого качества, чем березниковская - она без претензий проходит строжайший входной контроль качества на ВСМПО. Общая мощность цеха - 5 тыс тонн в год. Но увеличение производства относительно нынешнего, по словам Андрея Патракова, будет зависеть от роста потребностей рынка и цен на губчатый титан.
СМАРТФОН С ПРИВЕТОМ ИЗ СОЛИКАМСКА /strong>
Так откуда же на магниевом заводе взялся тетрахлорид титана? Оказывается, в виде побочного продукта от ещё одного уникального производства, аналогов которому нет не только в России, но и в мире. Без малого 45 лет назад, в декабре 1971-го, на СМЗ был введён в работу цех №7 - химико-металлургический.
С аналогичным подразделением «Ависмы» его роднит только общий принцип технологии - выделение из рудного концентрата полезных металлосодержащих компонентов путём хлорирования в расплаве солей.
Только вот основной целью химико-металлургического цеха на Соликамском магниевом является не столько титан, сколько тантал, ниобий и другие редкоземельные металлы. Эти элементы получают из лопарита - минерала, добываемого только на Кольском полуострове. Почему лопаритовый концентрат нужно везти с севера России на Урал, рассказал главный технолог ПТО СМЗ Игорь Ерёмин.
Игорь Ерёмин: - Технологию вскрытия лопарита хлорированием разработали ещё в 1960-х годах на опытном заводе института ГИРедМет в Подольске. Но разместить в Подмосковье большое производство с вредными выбросами в атмосферу и необходимостью куда- то девать радиоактивные материалы было невозможно. А куда? Естественно, на Урал. Причём туда, где есть много лишнего хлора. А тут Соликамский магниевый.
Не вдаваясь в тонкости технологии, поясним, что лопаритовый концентрат загружается в хлоратор, где при температуре 1050° С происходит вскрытие концентрата. При этом хлориды титана, тантала и ниобия покидают агрегат в виде парогазовой смеси, направляясь на дальнейшее разделение и переработку, а редкоземельные металлы выводятся в виде расплава. Остывший расплав растворяют, освобождают от радиоактивных тория и радия, затем также перерабатывают. Радиоактивный остаток отправляется для захоронения на специальный полигон в надежде, что когда-нибудь он будет во- стребован промышленностью.
Разумеется, получив технологию от учёных в начале 1970- х годов, специалисты опытного цеха её усовершенствовали. Ведь поначалу из лопарита получали лишь радиоактивные концентраты соединений ниобия, тантала и редкоземельных элементов, которые отправлялись на дальнейшую переработку на предприятия Казахстана.
Однако к середине 80-х годов на заводе научились выпускать соединения ниобия и тантала различной номенклатуры и чистоты, вплоть до категории «особая чистота», а в начале 2000-х началось производство карбонатов РЗЭ.
Андрей Анисимов, начальник цеха №7: - В год мы перерабатываем порядка 8,5 тыс тонн концентрата. Конечная продукция цеха - карбонаты и оксиды редкоземельных элементов, пента- хлориды тантала и ниобия - перерабатывается в готовую продукцию высокой чистоты в других цехах. То, что получается в итоге, буквально с колёс расходится в десятки стан мира - США, Австрию, Швецию, Японию, Китай, Индию. К примеру, ни один сенсорный экран смартфона или другого гаджета не будет чувствовать прикосновения пальцев без соединений ниобия. В наших планах увеличивать объёмы, расширять номенклатуру и повышать качество продукции. Но пока перспективы ограничены мощностями Ловозёрского ГОКа.
Впрочем, главная ценность цеха, по словам Анисимова, - не дорогие редкие металлы, а уникальные кадры, настоящий сплав профессионалов, который рождался прямо на промышленных площадках, поскольку ни одно учебное заведение не готовит ни печевых, ни аппаратчиков, способных работать на оборудовании, не имеющем аналогов в мире. Хотя к этим словам вполне могут присоединиться руководители всех основных цехов СМЗ. Вот такой он уникальный - «старший» брат «Ависмы» .
Опубликовано: корпоративная газета "Металлург"
+ Иная газета

Иная газета - Город Березники. Информационно-аналитический ресурс, ежедневные новости Урала и России.

цветная металлургия
-
На участке подготовки проб и механических испытаний титана центральной лаборатории комбината начался монтаж двух новых электродуговых вакуумных печей
-
Очередной конкурс профмастерства под эгидой молодёжной организации прошёл в ОПУ- 1 цеха №37
-
Последний месяц зимы, хоть и был длиннее на день, не доставил комбинату никаких «високосных» проблем
Читайте сегодня
- Пермяк добился ремонта своего дома через суд
- Более 5 тысяч пенсионеров Пермского края получат компенсацию взносов на капитальный ремонт.
- Сергей Будалин присвоил 2 миллиона рублей честных и ответственных березниковцев.
- В эти выходные состоится традиционная Строгановская регата
- Дом разваливается, а управляющая компания слилась из города
- Лето в городе: активный отдых в "Снежинке"
- Внимание: в Березниках планируется отключение воды на сутки
- Скоропостижно скончался атаман Марамыгин