"Ависма" работает по принципу "только вперёд!"
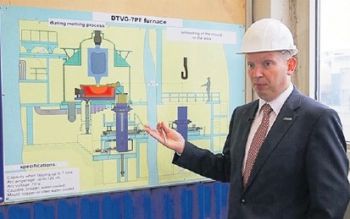
28 октября зрители канала Malina (РБК) могли увидеть программу «Сделано в России. Урал» с участием генерального директора корпорации ВСМПО-Ависма Михаила Воеводина, который лично провёл съёмочную группу по цехам завода в Верхней Салде.
«Сделано в России. Урал» - это региональный аналог федеральной программы об отечественных производителях, продукцией которых может гордиться страна. Программа даёт возможность увидеть, что такое современная российская промышленность, и убедиться, что она давно шагнула из советского прошлого в новое технологичное будущее.
История Верхнесалдинского металлургического производственного объединения началась летом 1933 года, с пуска под Москвой завода №45 - основного поставщика полуфабрикатов из алюминия и его сплавов для советского самолётостроения. Уже к 1940 году выпуск продукции вырос в четыре раза.
Динамичное развитие приостановили первые бомбардировки завода в июле 1941 года. Тогда было принято экстренное решение о строительстве завода-дублёра на Урале, в Верхней Салде. Весной 1942 года объём производства достиг довоенного уровня, а в 1943-м проектная мощность выросла в шесть раз, что позволило полностью обеспечить потребности военной авиации, судо- и танкостроения, производства боеприпасов и вооружения. Со временем от завода потребовалась иная продукция - так началась работа с титаном.
Михаил Воеводин: «После распада СССР практически встали все предприятия - наши потребители, и ВСМПО тоже было на грани остановки. Выживание пошло по двум направлениям. Первое - локальное выживание за счёт продукции из ферротитана: посуда, лопаты - то, что позволило сохранить и специалистов, и город, и предприятие. С другой стороны, руководством в 1993 году было принято единствен- но правильное решение - выход на внешний рынок. ВСМПО под руководством Владислава Валентиновича Тетюхина стало его реализовывать».
С 1993 года началась эра ВСМПО как экпортоориентированного предприятия. Титанических усилий стоил корпорации путь от экспорта простой продукции в виде слитков до сертификации компании как стратегического партнёра Boeing и Airbus по продукции глубокой переработки с высокой степенью добавленной стоимости: штамповки и штамповки после механообработки. Сегодня это 60% всей выручки корпорации.
Михаил Воеводин: «Если вдруг нарушатся производственные цепочки ВСМПО-Ависма с Boeing и Airbus, больно будет всем. Boeing и Airbus придётся искать нового поставщика, а нам - новые рынки сбыта. Эти кооперационные экономические цепочки связывают наши государства, потому что ни одной бизнес-единице не выгодны политические турбулентности».
Но сегодня и для людей, и для продукции ВСМПО-Ависма никакие турбулентности не страшны. На ВСМПО работают более 14 тыс сотрудников - треть всего населения Верхней Салды, а вместе с Ависмой и её дочерними предприятиями это более 20 тыс человек.
Годовые затраты корпорации на социальную сферу - порядка 1 млрд руб. Действует большая программа поддержки ветеранов труда обоих заводов. По словам Михаила Воеводина, «…это вообще обязательная вещь, это наше спасибо всем, кто сделал всё хорошее для корпорации».
Кстати, обойти все цехи ВСМПО даже за целый день невозможно. Здесь можно про- вести неделю, как в Лувре или Эрмитаже. За работой одного только гигантского пресса усилием в 75 тысяч тонн можно наблюдать часами.
Таких прессов во всём мире два: один - на совместном предприятии с Alcoa в Самаре, второй - на ВСМПО. Именно на нём в 1974 году была изготовлена переходная втулка для советско-американского космического корабля «Союз-Аполлон», а в 2003 году - самая крупная штамповка (опора шасси) для самолёта А380. Далее путь съёмочной группы лежал в совсем новый производственный комплекс.
Михаил Воеводин: «Сейчас мы находимся на территории комплекса, где будут расположены 10-15 печей и пресс усилием 4 тыс тонн. Это новый комплекс, он ещё даже не введён в эксплуатацию. В настоящий момент здесь идут пусконаладочные и испытательные работы. Введение пресса 4-тонника в работу позволит увеличить производство нашего TOP- продукта - штамповок после механообработки. Мы инвестировали в этот комплекс в течение пяти лет более 80 миллионов долларов».
Этот комплекс - один из трёх крупнейших инвестпроектов, работа над которыми велась в корпорации ВСМПО-АВИСМА с 2007 года. Тогда была разработана инвестпрограмма в $1 млрд на период до 2012 года. Кризис 2008 года внёс свои коррективы, производство упало на 40%, но инвестпрограмма не останавливалась ни на день, хотя вместо планируемых $200-250 млн в год, в то время вкладывалось по $100-120 млн. Следующим проектом стал комплекс новых гарнисажных печей.
Михаил Воеводин: «Исторически мы имеем у себя две гарнисажные печи с развесом слитка 4,5 тонны. Новые печи дают слиток большего развеса - порядка 7 тонн. Основное достоинство гарнисажных печей по сравнению с вакуумно-дуговыми - это то, что они дают возможность гарантированно получить суперчистый материал».
Важность гарнисажных печей на производстве Михаил Воеводин прокомментировап простым, но очень наглядным примером. Каждый знает, что в современных ручках есть шарик, который, в основном, производится из вольфрама. Это тугоплавкий металл, и в ходе переплавки с титаном он не расплавляется. Соответственно, если процесс получения титановых слитков идёт в вакуумно-дуговых печах, то этот шарик останется в слитке.
Конечно, технологии ВСМПО обеспечены всеми средствами контроля, чтобы этого не случилось, и в конечном итоге шарик специалисты обязательно обнаружат. Но если предположить, что он не будет найден.
Что же произойдёт? Шарик попадёт в штамповку, которая окажется в двигателе самолёта и станет центром напряжения, и со временем - через год, два, три - лопатка двигателя, которая будет сделана из этого титана, разрушится. Разрушается двигатель - разрушается самолёт. В гарнисажных же печах, в отличие от вакуумно-дуговых, этого никогда не случится. Даже самое малое вкрапление останется в гарнисаже - бетонном саркофаге.
Михаил Воеводин: «Так как плавка титана - взрывоопасный процесс, все вакуумно-дуговые печи находятся в бронекожухах, а гарнисажные - в бетонном саркофаге: три бетонные стены и одна стеклянная. Если внутри возникает нештатная ситуация, во время плавки в этом саркофаге никто не находится, а взрывная волна уходит в стеклянную стену и гасится. После неё есть ещё одна лёгкая стена, которая выносится этой взрывной волной. Дальше находится «болото», хождение по которому запрещено. Въездные ворота в этот саркофаг весят 8 тонн».
Порядка 85% оборудования и технологий, используемых в этом комплексе, - российского производства. Печи разработаны в Верхней Салде - научно-исследовательский центр завода насчитывает порядка 900 сотрудников, которые и создают новые сплавы и технологии. А произведены печи в Новосибирске. Одна же из уникальных установок, единственная в мире, создана по спецзаказу на предприятии «Машпром» в Екатеринбурге.
Установка по специальной программе моет крышку гарнисажной печи изнутри струями воды под давлением 1700 атмосфер. Следующим на пути съёмочной группы был опять совершенно новый технологический комплекс, аналогов которому нет в России. Он состоит из кольцераскатного стана, эспандера, пресса усилием 8 тысяч тонн и большого количества печей. И если на прежнем стане на ВСМПО выпускались кольца до 2,7 м в диаметре, то на новом - до 3,5 м в диаметре и до 0,8 м высотой. А это, в свою очередь, новые детали для космических ракет, спутников и авиации, новые заказы, новые мощности, ведь практически все мировые авиастроители являются партнёрами корпорации ВСМПО-Ависма: Boeing, Airbus, Embraer, Rolls Royce, Goodrich и более 300 других.
«Только вперёд!» - этот принцип работы корпорации определил ВСМПО-Ависма ведущую роль на мировом рынке изделий из титана. Сегодня корпорация закрывает 40% потребностей в титане Boeing, 50% - Airbus и 100% - Embraer. В планах компании, как подчеркнул её генеральный директор Михаил Воеводин, - увеличить производство к 2020 году на 40%.
Опубликовано: корпоративная газета "Металлург"
+ Иная газета

Иная газета - Город Березники. Информационно-аналитический ресурс, ежедневные новости Урала и России.

цветная металлургия
-
На участке подготовки проб и механических испытаний титана центральной лаборатории комбината начался монтаж двух новых электродуговых вакуумных печей
-
14 марта 1936 года на соликамском магниевом заводе был произведён первый магний-сырец, и отлита первая чушка из него
-
Очередной конкурс профмастерства под эгидой молодёжной организации прошёл в ОПУ- 1 цеха №37
Читайте сегодня
- Пермяк добился ремонта своего дома через суд
- Более 5 тысяч пенсионеров Пермского края получат компенсацию взносов на капитальный ремонт.
- Сергей Будалин присвоил 2 миллиона рублей честных и ответственных березниковцев.
- В эти выходные состоится традиционная Строгановская регата
- Дом разваливается, а управляющая компания слилась из города
- Лето в городе: активный отдых в "Снежинке"
- Внимание: в Березниках планируется отключение воды на сутки
- Скоропостижно скончался атаман Марамыгин